Hybrid CFD simulation of two-phase flow in inline flow splitters using VOF and Lagrangian models
The current PhD work is part of the European project TOMOCON which joins 12 international academic institutions and 15 industry partners who work together in the emerging field of indus- trial process control using smart tomographic sensors. Four industrial processes are investigated experimentally and numerically, inter alia, inline fluid separation [1]. This recent technology for oil/gas extraction makes use of a static swirl element installed inside the pipeline (see Fig. 1) and which has a bullet form with deflected blades on its surface to transform part of the incoming axial momentum into a tangential one. This flow splitter can generate centrifugal forces up to 100 times the gravitational acceleration and separate the phases leaving the heavy phase next to the wall and the light one in the center to be recovered at the outlet by a pick-up tube.
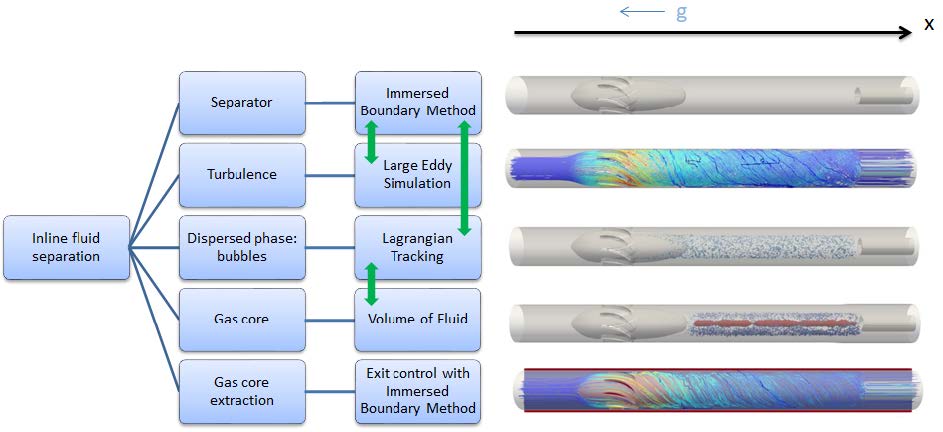
In the present work, we are interested in developing hybrid CFD methods in the IMFT in-house code JADIM to simulate the two-phase flow separation [2]. Since the scales are ranging from meters the length of the device (pipe, swirl element) to a millimeter which is the size of the smallest bub- bles and drops, the numerical strategy needs to combine Eulerian and Lagrangian schemes. First, because of the complexity of the separator geometry, we use Immersed Boundary Method (IBM)
[3] for solid/fluid interaction to simulate the pipe, the swirl element and the pick-up tube. The flow being highly turbulent that Direct Numerical Simulation (DNS) is not possible, Large Eddy Simulation (LES) is considered and the turbulence is modeled using mixed dynamic Smagorinsky model [4]. Then the Lagrangian solver [5] is used to track the dispersed phase (drops/bubbles).
Once the separation is done and the accumulation of the dispersed phase takes place leading to large volume of gas/oil compared to the mesh size, we switch to the Volume of Fluid (VoF) [6] method to simulate the core inside the heavy phase. Finally, the control of the exit condition for the light phase extraction is done through the flow straightener placed between the pipe and the pick-up tube using Immersed Boundary Method.
To ensure a good interaction/communication between the CFD methods considered here, a coupling of the solvers is needed. Therefore, to be able to use Large Eddy Simulation (LES) on a coarse mesh and avoid the constraint of mesh refinement next to the IB wall, an original stochastic wall model is developed for hybrid LES/IBM [7] and validated through the study of the classical turbulent pipe flow. The Lagrangian Tracking solver is also coupled to Immersed Boundary Method to enable the rebound of the bubbles/drops on the surface of the IB solids via a collision model. The hybrid Lagrangian Tracking/Volume of Fluid consists in moving the bubbles/drops in contact with a VoF cell or those which have migrated to the separator center from the Lagrangian framework to the Eulerian one and updating the phase fraction with their corresponding volume. The method is validated by simulating bubbles accumulation in a rotating flow.
The numerical strategy based on the coupling of these different methods makes possible accurate simulations of the inline separation with limited CPU cost. A full description of single-phase flow in the separator is done, the velocity and pressure profiles are plotted, a swirl number is calculted and its evolution in the streamwise direction is fitted with a previous experimental correlation. Two-phase flow separation is then simulated, the bubble migration is described and the gas core is characterized. The effect of the Reynolds number and the condition at the pick-up tube are also studied. The numerical simulations help fixing the physical parameters which influence the separation and control the efficiency and validating models with experimental data from TU Delft, HZDR and TU Lodz.
Keys words: CFD, Inline fluid separation, Swirl, IBM, LES, VoF, Lagrangian Tracking.
Acknowledgements
This work is done within the TOMOCON project which has received funding from the European Union’s Horizon 2020 research and innovation program under the Marie Sklodowska Curie grant agreement No 764902.
References
- Sahovic B., Atmani H., Sattar M. A., Martinez Garcia M., Schleicher E., Legendre D., Climent , Zamansky R., Pedrono A., Babout B., Banasiak R., Portela L.M., and Hampel U. Controlled inline fluid separation based on smart process tomography sensors. Chemie Ingenieur Technik, pages 92/5, 1–11, 2020.
- Atmani H., Zamansky R., Climent E., and Legendre D. Cfd approach to simulate two phase flow inline-separator coupling ibm, les, lagrangian tracking and vof methods. In SINTEF Proceedings 6,
- Bigot B., Bonometti T., Thual O., and Lacaze L. A simple immersed boundary method for solid fluid interaction in constant and stratified density J. Computers and Fluids, 2014.
- Calmet I. and Magnaudet J. Large eddy simulation of high schmidt number mass transfer in a turbulent channel Physics of Fluids, 1997.
Supervisors: Dominique LEGENDRE, Rémi ZAMANSKY, Eric CLIMENT